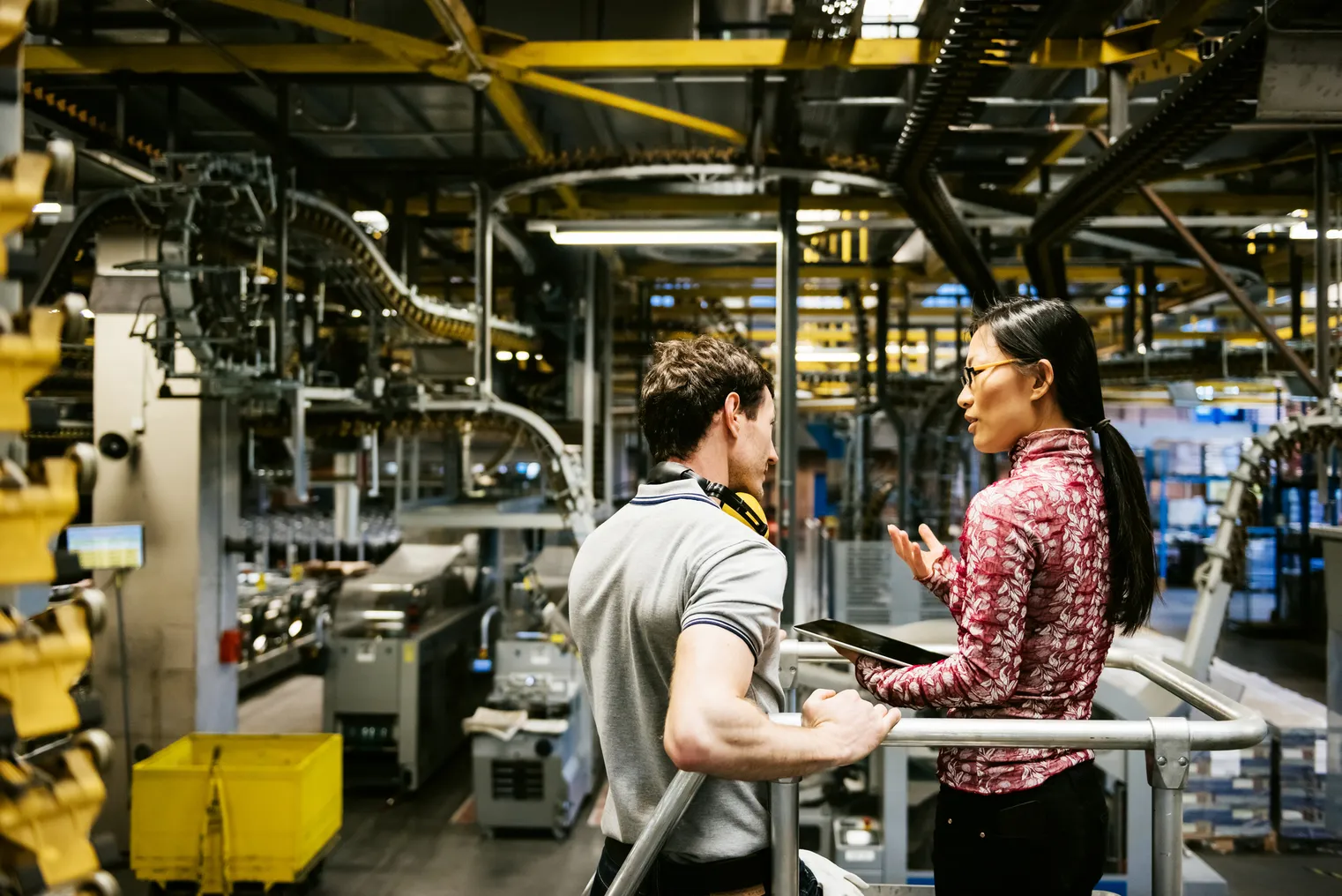
Manufacturing could be short 1.9M workers if the talent gap isn’t fixed
Manufacturing is shooting past its pre-pandemic norms.
The industry, aided by both massive private and public investments, has seen huge gains in employment and capital spending on new projects in the last five years.
Employment reached 13 million as of January 2024, while the number of manufacturing establishments in the U.S. rose by more than 11% between the first quarter of 2019 and the second quarter of 2023, reaching 393,000.
And yet, the industry is staring down a major obstacle to all that growth — labor.
An April 2024 report from Deloitte and the Manufacturing Institute claims that manufacturers could need as many as 3.8 million new workers by 2033. Roughly 1.9 million of those could go unfilled if current labor gaps remain unsolved.
Check out our five top takeaways from the report on the industry's impending job gap and companies’ efforts to address it.
1. Manufacturers need workers at every level, but especially in technical roles
In reviewing five years of job posting data, researchers found a 75% jump in demand for simulation and simulation software skills, mainly for technology-enabled production or testing roles. These technical roles that can leverage the integration of connected devices, equipment and systems are likely to grow the fastest between 2022 and 2032, according to the report.
The number of industrial machinery maintenance technicians, which made up 270,000 manufacturing workers in 2022, are slated to jump by 16% by 2032. And in production roles, the fastest-growing segment is for highly technical roles, such as semiconductor-processing technicians and electronics and electromechanical assemblers.
2. Higher education needs to adapt to changing demands
Across the country, the number of associate degrees awarded has stagnated over the past decade as more people turn to certificates as an alternative option to gain training for skilled trades.
The report found that the average growth in certificate awards was more than four times the growth in associate degrees for manufacturing-related programs between 2011 and 2022.
That shift is in line with the Biden administration's push for the industry to offer more jobs that don't require college degrees.
But while certificates could help grow the talent pool for foundational industrial knowledge, the report claims that it could leave a gap in those qualified for higher level technical roles.
It begs the question of how colleges continue to prove the vitality of bachelor's and associate's degrees in fields like computer and information sciences and engineering, which can help give individuals the technical skills companies need.

3. Workers want flexibility — or they'll look elsewhere
Gen Z and millennial workers are more likely to switch jobs than previous generations.
Like in many industries, companies are finding flexibility and remote-work options are two of the most impactful ways to attract and retain employees. Nearly half of survey respondents noted that flexible work arrangements, including flexible shifts, shift swapping or split shifts, is a strategy they've used successfully to retain workers.
In addition to flexible schedules, workers also want affordable and available childcare. The issue has become so important that more companies are beginning to offer it onsite or to subsidize childcare costs.
Above all though, companies listed competitive benefits as the best way to attract and retain employees. This could include not only competitive wages but paid time off, robust health care and ample parental leave.
4. Manufacturers prioritize training to keep workers
Companies are focusing more on training and re-skilling workers in a bid to keep them on the job. Many are offering mentoring and rotational programs for new hires to help them receive well-rounded skills development.
In addition, internal training programs are proving vital to help employees adapt to new technologies, according to the report. Skills assessments are then helping employees to track their progress.
Manufacturers can also leverage digital tools like tablets and smartphones to do on-the-job training and performance maintenance.

5. Companies need to "broaden the aperture" on the talent pool
Manufacturers are increasingly partnering with community organizations and educational institutions to recruit workers. Nearly all of those surveyed said they are forming at least one partnership to improve recruitment and retention, and many are partnering with four or more organizations.
At the same time, Manufacturing Institute President and Executive Director Carolyn Lee noted in an interview that companies need to "broaden the aperture" to look at more populations and communities across the U.S. to bring people into the industry. This could include people such as mothers who left the workforce during the pandemic, refugees, formerly incarcerated individuals or those with cognitive disabilities.
"How do you bring people who are on the sidelines back in and what are the pathways?" Lee said. "There is this broader vision around what you need to do to be able to attract and retain that workforce.”