In a 60,000-square-foot warehouse on Wichita State University's campus, several of the country's biggest tech companies have set up shop to create next generation manufacturing innovations.
Established in June 2022 and led by Deloitte, The Smart Factory focuses on both training young engineers and working with a host of clients to solve production and process challenges using solutions developed and advanced onsite.
The project is based around an ecosystem of more than 20 partners to collaborate on smart production processes. Founding partners include Siemens, Dragos, Amazon Web Services, SAP, Infor and Wichita State.
The site is an example of the partnerships universities, consultants, manufacturers and others are forging to bring forth new technologies and benefit the industry.
Work at The Smart Factory is centered around advancing eight use cases in smart manufacturing, including factory asset intelligence/performance management, engineering collaboration/digital twins, plant consumption and energy management, quality sensing and detection, factory synchronization and dynamic scheduling, augmented workforce efficiency, smart conveyance and smart warehousing solutions.
External companies can then visit the factory and explore solutions that can be integrated into their own operations, an in-depth process that takes up to eight weeks of planning, said Ken Hall, Siemens program director and digital enterprise solutions architect who is stationed at the factory. Visiting companies include those from aerospace, food and beverage, electronics and soon semiconductors.
As part of the factory, the company and Deloitte operate a dedicated digital twin R&D space. One of the space's projects is the creation of a digital twin of the factory's in-house manufactured smart Rover education kits.
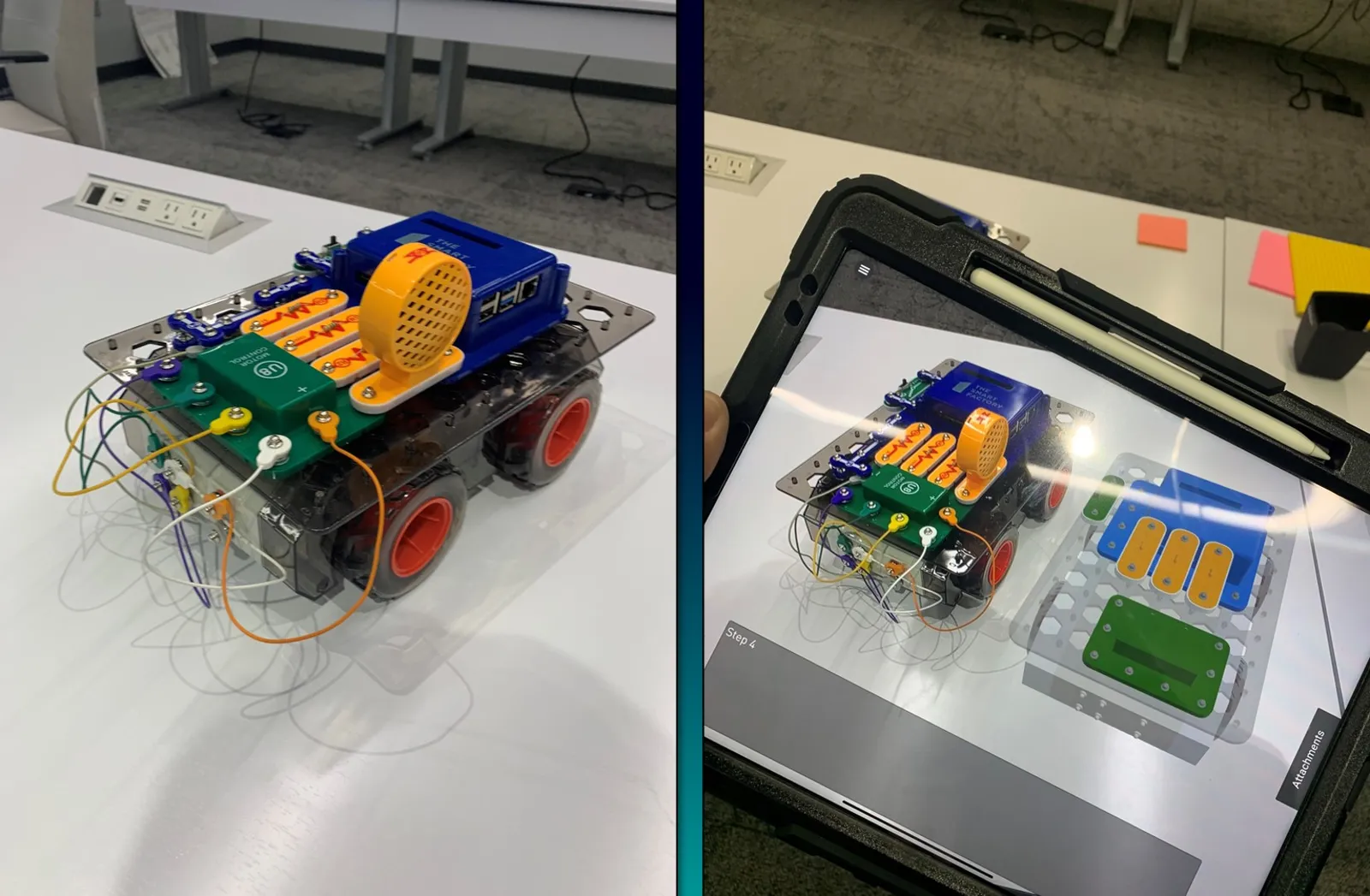
The Rover kits are later donated to area schools, but Siemens first created the digital models to demonstrate the use of digital twins in practice to simulate how to improve its system before making any physical changes, an application it also shares with companies looking to use the same solution at their own sites, Hall said.
As another way to showcase the use of 3D modeling, The Smart Factory created a digital twin of its own facility and is developing another to simulate its energy usage, Hall added.
Digital twins are a key part of The Smart Factory's work given their many applications for companies, whether to make improvements on the shop floor to boost efficiency, improve quality control or to better monitor their onsite energy usage, said Brian Meeker, leader of Deloitte's U.S. product engineering and development practice.
But while the use of 3D models is becoming an increasingly common tool used during R&D design processes, Meeker noted that fewer companies have integrated the technology more holistically throughout the manufacturing process to become a model-based enterprise throughout engineering and manufacturing.
Digital twins can be used to model each machine on a shop floor and simulate manufacturing processes and use cases, he added. Such integrations are ones that companies can learn how to undertake at The Smart Factory.
"And the big leap when I integrate all this data together, and I become one of those few companies that have models used for both engineering and manufacturing, I can now launch a product virtually," Meeker said. "And I can see exactly what the product's going to be and virtually simulate the whole manufacturing process to make sure I'm not only going to build it but I'm going to build it flawlessly.”
The recent influx of new manufacturing projects announced in the U.S. over the past year also gives many companies a chance to integrate new technologies and capabilities into a site, said Bill O’Neill, head of Siemens’ Digital Enterprise Center of Competence, Americas. Companies building new sites are also being pushed to use solutions like digital twins to help them produce goods faster and more efficiently.
“Greenfields represent an amazing opportunity for a company because they have a chance to really do things in ways they might always have dreamed of and wanted to do, but have been limited by the infrastructure and legacy equipment systems,” O’Neill said. “ ... We have the capability and the resources across the ecosystem to really sit down and workshop how to plan a facility for ultimate flexibility or other key drivers.”