Tim Robertson is the CEO of DHL Global Forwarding Americas. Opinions are the author’s own.
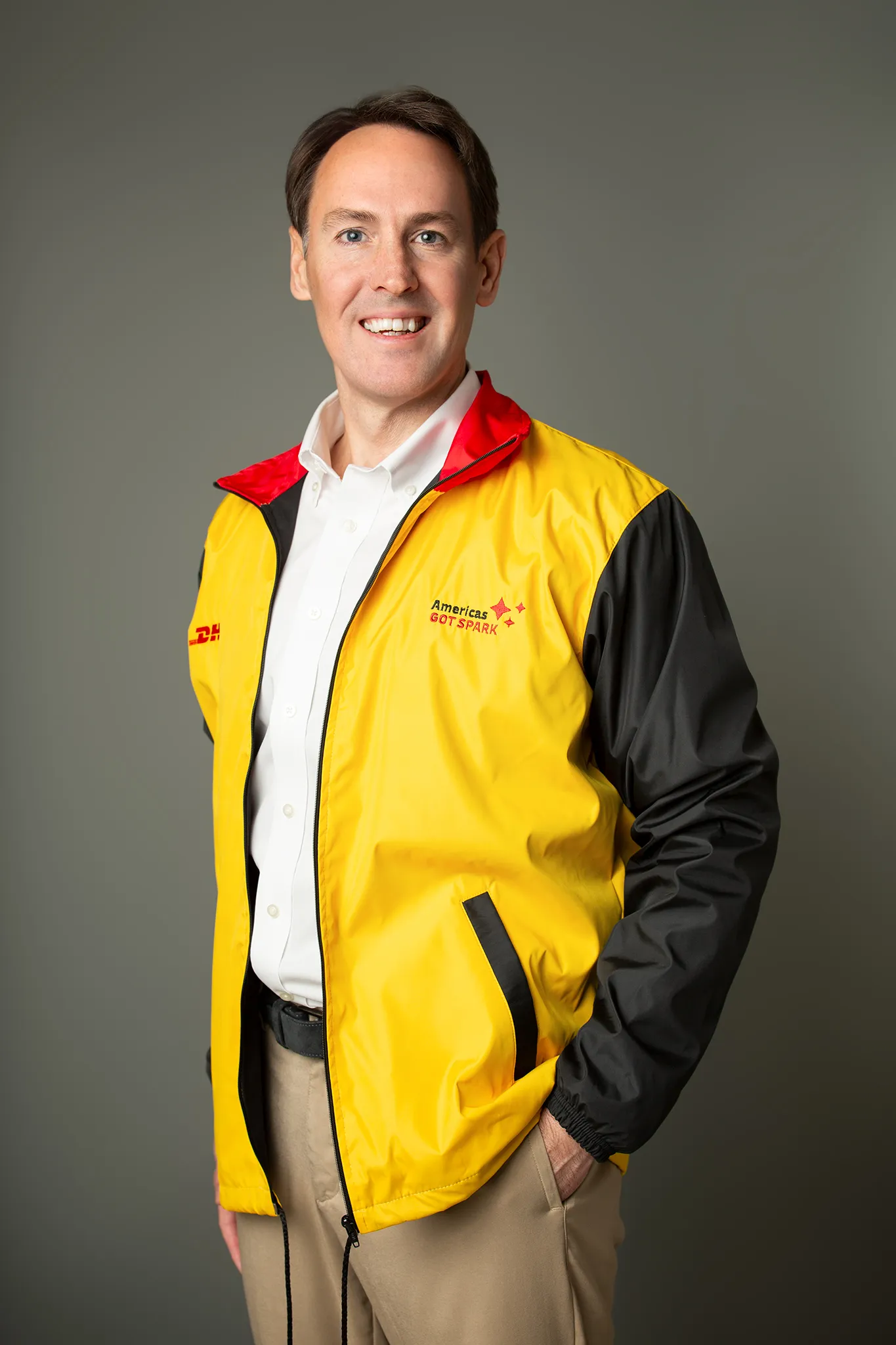
Semiconductors are to the 21st century what oil was to the 20th: a foundational element of modern technology and industry. Yet, during the peak of the China-West economic partnership, the critical importance of semiconductors often went unnoticed.
Taiwan secured a dominant position in global production. Now, with cooling relations between Beijing and Washington and similar tensions in Europe, this has led to what many describe as a new "arms race,” the "chip war" or "Cold War 2.0."
This economic clash coincides with multiple global crises. The world is still recovering from a historic pandemic, while wars raging in Europe, such as the Israel-Hamas war and the Russia-Ukraine war, further exacerbate disruptions. The Red Sea conflict and the Panama Canal drought also add to the turmoil.
Simultaneously, the world is moving towards evermore advanced technology, making future demand for semiconductors a dead certainty. Looking at both the demand and disruptions highlights the necessity for robust and resilient supply chains. However, the present strain on existing semiconductor supply chains is minimal, presenting an opportunity to build and stress-test these vitally important links.
Building semiconductor fabrication plans requires massive logistical coordination. A new fab demands 200,000-500,000 square feet of warehousing space, an extensive workforce and the transport of 300,000-450,000 tonnes of cargo. This equates to approximately 10,000-12,000 truckloads, 6,000-8,500 container shipments, 10-20 breakbulk charters, and 300-500 airfreight shipments, according to DHL Global Forwarding Americas.
Meeting customer timelines while staying efficient, optimized and under budget is a significant challenge.
To achieve these ambitious goals, adopting advanced tools and best practices is crucial. Enterprises can leverage AI to optimize various aspects of semiconductor production, such as yield optimization, predictive maintenance and process automation.
By harnessing AI algorithms, companies can improve production efficiency and reduce costs. Establishing end-to-end visibility in the supply chain can provide real-time insights into inventory levels, supplier performance and demand fluctuations, enabling proactive decision-making.
Accurate demand forecasting is critical. Building strong relationships with suppliers and partners ensures a resilient supply chain too.
The CHIPS and Science Act, a nearly $53 billion initiative, aims to reinvigorate the domestic semiconductor industry. However, the challenges are immense: competing nations are ramping up their investments, and the cost of building state-of-the-art fabs remains high.
The success of such initiatives depends not only on current subsidies, but also on sustained future funding and strategic tax incentives. Thanks to the CHIPS Act, the U.S. share of global fab capacity is forecasted to grow from 10% today to 14% by 2032, according to a Boston Consulting Group and Semiconductor Industry Association report.
This modest increase underscores the fierce state of global competition and the need for continued investment in the semiconductor sector. Additionally, Intel, one of the world’s oldest chipmakers, is finalizing details with the Department of Commerce for an $8.5 billion investment to support its modernization and new-build projects, an effort that enjoys strong bipartisan support.
But these financial investments are only part of the solution. Education and workforce development remain crucial for fostering a future-ready talent pool in semiconductor technologies. Equally important is the need for a diversified supply chain strategy, as demonstrated by the recent surge in global semiconductor investments.
In the U.S., roughly 80 new semiconductor manufacturing projects have been announced since the passage of the CHIPS Act, according to SIA, indicating a significant push to localize production capabilities.
Other countries are doing the same. South Korea plans to invest $471 billion through 2047 to build 16 new fabs in a mega chip cluster in Gyeonggi Province, while Europe has seen seven major wafer fab investments since 2020.
Costa Rica, often referred to as the “Silicon Valley of Latin America,” is also becoming a key player in the semiconductor supply chain, with Intel announcing a $350 million investment to expand its semiconductor assembly and testing operations there. This geographic diversification of supply chains is crucial for enhancing resilience against geopolitical risks and ensuring a steady supply of semiconductors to meet growing global demand.
The global investments in semiconductor manufacturing — spanning the U.S., South Korea, Europe and Costa Rica — are fundamentally reshaping supply chains by decreasing dependency on Taiwan's production capabilities. With new fabs being built and advanced manufacturing technologies being adopted, these regions are enhancing local capabilities, increasing production capacity and creating redundancies that mitigate risks from geopolitical tensions and natural disasters.
Companies must optimize their supply chain strategies by incorporating multi-sourcing from new hubs and investing in advanced tools for visibility and predictive analytics. Additionally, they must align with local regulations and standards to ensure operational continuity and resilience in the increasingly complex and decentralized semiconductor ecosystem.
The importance of acting now cannot be overstated. Future demand for semiconductors is certain, and the current lack of strain on supply chains offers a crucial window to build and stress-test these networks with robust government support, ensuring long-term returns.
Achieving semiconductor self-reliance will depend on strategic partnerships and navigating geopolitical and logistical complexities. By adopting advanced AI-driven strategies and best practices, the industry can optimize efficiency, manage risks and meet increasing global demand.
Moreover, fostering open trade and diversifying markets through trade agreements and collaboration will not create a new semiconductor "superpower," but will instead enhance supply chain resilience and mitigate disruptions by expanding global production capabilities — essentially embracing an omnishoring strategy.