Editor’s note: This article is the third installment of a three-part series exploring the push to rid the U.S. manufacturing industry of PFAS. Read the second installment on PFAS in firefighting foam and the first installment on PFAS in food manufacturing.
Buy a pair of Levi’s jeans, a Home Depot rug or Fenty Beauty makeup, and the brands all have a common claim — the products are PFAS-free.
Brands like these are among a growing number of household names claiming to have rid their supply chains of per- and polyfluoroalkyl substances.
Levi Strauss & Co. for instance, banned the use of PFAS in its apparel in 2018. The clothing manufacturer developed a “restricted substances list” that bars certain chemicals from production and set new standards for wastewater leaving supplier facilities.
The manufacturer phased out PFAS from all products, and ultimately discontinued some apparel items that relied heavily on the chemicals for performance, such as its Commuter jean line, Linda Gallegos, senior design innovation lead at Levi Strauss, said in a Wall Street Journal podcast interview in 2023.
Levi’s is one model of how to rid a manufacturing supply chain of PFAS, but undertaking the process can be arduous. Many companies get stuck before the project even begins — they don’t know if their products contain forever chemicals, and they lack visibility into their supply chains to identify where a source of contamination could exist.
But with rising consumer concerns and increased PFAS regulations, more manufacturers are considering auditing their supply chains to determine the presence of forever chemicals. The question for many is: How to start?
Admit ‘I probably have PFAS’
The presence of PFAS in a product is often the result of its existence in components or raw materials far up the supply chain. But for companies that lack visibility into tier 2 and tier 3 suppliers and beyond, it can be difficult to know if the item they ultimately sell contains one of the thousands of variations of PFAS.
“You can’t do anything about PFAS in your products if you haven’t looked and identified where they are,” said Neil Smith, global compliance and sustainability director at computer and electronics manufacturer Noco.
Taking on such an endeavor can be hefty, with coordination needed between multiple levels of product designers, manufacturers and suppliers.
For anybody dealing with PFAS, the very first thing to do starting out is to adjust your mindset completely and say ‘I probably have PFAS.’

Neil Smith
Global Compliance and Sustainability Director at Noco
“The first step in treating your problem is acknowledging you have a problem. For anybody dealing with PFAS, the very first thing to do starting out is to adjust your mindset completely and say ‘I probably have PFAS,’” Smith said.
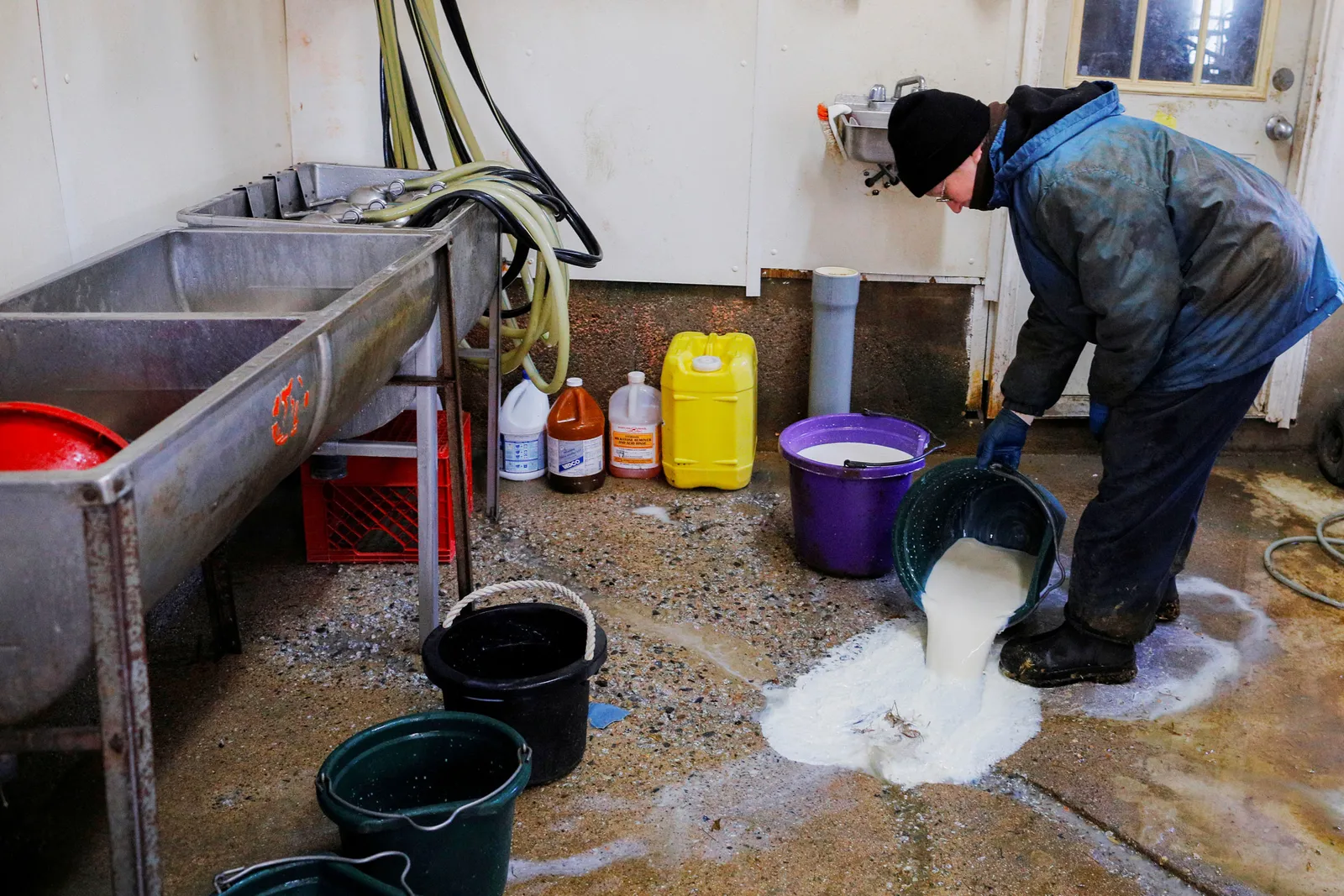
Breaking down the audit process
The audit process is a multi-step strategy that begins with setting chemical use standards, said Aditya Vedantam, associate professor of operations management and strategy at the University of Buffalo. The first thing any manufacturer should do is create a PFAS policy outlining the company’s stance on forever chemicals and their allowable use, Vedantam added.
Such a policy should consider if products will be sold to multiple countries and jurisdictions, taking into consideration all relevant government policies. Manufacturers need to communicate that policy with their upstream suppliers to ensure compliance.
The next step is to fully map the supply chain and identify all suppliers, beginning with raw materials through to assembly and packaging. Mapping should include identifying the source of all raw materials.
“It’s important for manufacturers when they’re auditing to go beyond just the tier one, tier two suppliers, but to go deeper into their supply chain to find sources of PFAS,” Vedantam said.
The steps behind a PFAS supply chain audit
-
Step 1: Establish a PFAS policy
Develop guidelines that outline your company’s allowable levels of various chemicals, including PFAS.
-
Step 2: Map the supply chain
Identify all suppliers, including tier three and four supplies, for raw materials, packaging and components.
-
Step 3: Perform a risk assessment
Conduct screenings to identify suppliers at high risk of PFAS contamination.
-
Step 4: Engage with high-risk suppliers
Train and incentivize these suppliers on how to avoid contamination, including how to screen their own processes for PFAS.
-
Step 5: Continuous monitoring and improvement
Monitor your new processes and publicly report any instances of PFAS in your supply chain.
-
Step 6: Invest in alternative chemical development
Invest in R&D to find safe alternatives for the use of forever chemicals in your production.
Step three is engaging with suppliers that may be in danger of falling into noncompliance with a manufacturer's PFAS policy. Once those suppliers are identified, Vedantam said manufacturers should train them on compliance and regularly test samples to ensure those rules are followed.
Once these aspects of a supply chain audit are complete, manufacturers should continuously monitor and make improvements, as well as publicly report any presence of PFAS.
Finally, manufacturers can opt to invest in research and development to identify PFAS-free alternatives.
“Manufacturers need to recognize that PFAS regulations are inevitable and they are going to be affecting their supply chains sooner rather than later,” Vedantam said. “So proactively working to eliminate PFAS or reduce the use of PFAS in their supply chains can help quite a bit in terms of reducing the cost of operations in the future.”
What should an audit entail — and how much will it cost?
The costs, time and energy involved in manufacturing supply chain audits varies widely by company size and scope, particularly if using a third-party auditor, Smith said.
For companies that have tighter control over the design process and more robust engineering and R&D teams, Smith said it could be possible to keep the audit in-house. But for smaller firms or those that outsource more of these functions, an outside expert could be necessary.
Vedantam recommended manufacturers opting to hire an outside firm choose a well-established auditing company with a large customer base and established testing protocols and certification standards. Over time, he added, manufacturers can create more internal systems.
“Eventually, I think manufacturers may also develop their in-house capabilities for testing and pass it on to their suppliers to do routine checks. In the long run that may be more cost efficient for them,” Vedantam said.
What is the risk of not acting?
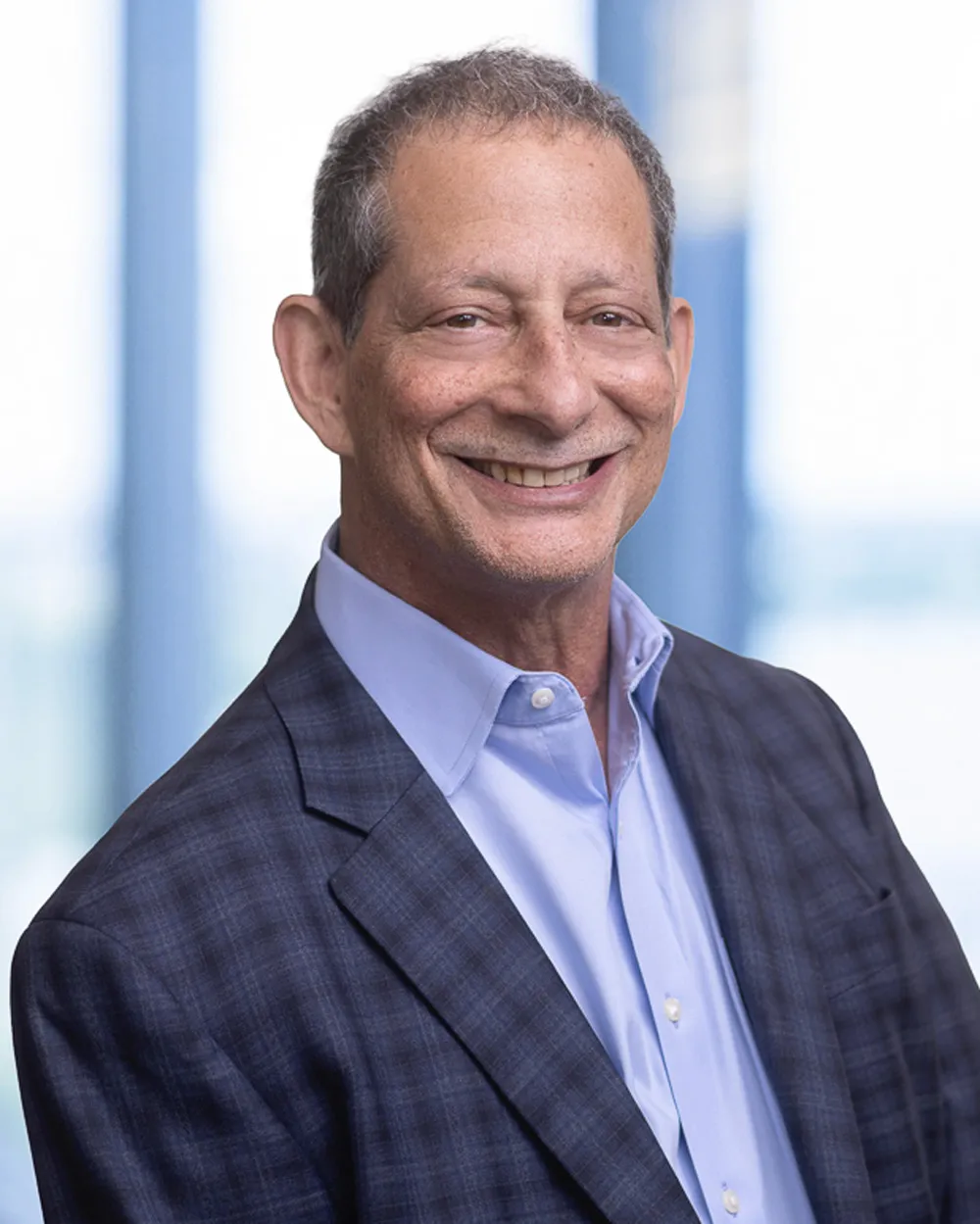
The reporting date for manufacturers to disclose the use of PFAS to the Environmental Protection Agency is currently set for January 2026. Given that, now is the time for companies to undertake the audit process, said Michael Blumenthal, an attorney at McGlinchey Stafford who specializes in PFAS litigation.
Doing so will not only better ensure manufacturers are compliant with federal and state laws, but can help ward off potential litigation.
While reporting deadlines could be subject to change under the incoming administration, President-elect Donald Trump’s nominee to lead the EPA, Lee Zeldin, has previously voted in favor of some PFAS regulations. This includes a 2021 bill that would have put some forever chemicals under a national drinking water standard.
The more oversight and regulation of PFAS continues to grow, the more liable manufacturers are becoming for chemicals that make their way into products, even if far up the supply chain, Blumenthal said.
This issue has taken on new importance after the EPA announced in April that it would now focus on using the Comprehensive Environmental Response, Compensation, and Liability Act to hold manufacturers responsible for “significantly [contributing] to the release of PFAS contamination into the environment.”
Knowing which forever chemicals are present and where will also help manufacturers better comply with the EPA’s new rule under the Toxic Substances Control Act, which will require companies beginning as soon as 2025 to report the presence of PFAS in their supply chains.
Manufacturers must report an increasing amount of PFAS use
“If you break it down, manufacturers are now going to be required to take certain steps before they accept a product from a supplier,” Blumenthal said. “If you’re somehow connected to the material, whether intentionally or unintentionally, you are going to be jointly and individually liable.”
Consumer litigation is a growing risk for manufacturers, with a rising number of lawsuits targeting manufacturers for failing to disclose the presence of PFAS in products, Blumenthal added. There are also increasing examples of manufacturers settling lawsuits related to PFAS contamination. In April, 3M finalized its $10.5 billion settlement with public water suppliers, and Dupont, Corteva and Chemours finalized their $1.2 billion settlement over PFAS contamination in February.
“Private party litigation is going to continue to hold manufacturers responsible and I think the government is going to be there, I think it’s only going to get ramped up,” Blumenthal said. “It would be prudent for manufacturers to really do a thorough inventory and know what PFAS they’re using and take precautions.”
Visuals Editor Shaun Lucas contributed to this story.