Dave Prezzano is the global head of Go-to-Market for HP Personalization and 3D Printing. Opinions are the author’s own.
Industries today are at an innovation crossroad. Challenges such as labor shortages, supply chain disruptions fueled by global insecurities, a rapidly evolving regulatory landscape and a looming recession threaten to pause investments in emerging technologies and digital transformation.
Yet, if manufacturers learned anything from the pandemic, it’s that sticking to the status quo and prioritizing short-term economic perspectives are no longer viable or competitive options in today’s context.
Rethinking logistics
Take our global supply chain as an example. Looking back, it was often additive manufacturing that allowed disrupted supply chains to quickly pivot, simplify and strengthen.
Reshoring has been ticking upwards as a result of the benefits of localized and on-demand production becoming “must have” in the years since the pandemic’s onset. This has been bolstered by the signing of laws such as the Infrastructure Investment and Jobs Act and the Inflation Reduction Act, which incentivize investment in the U.S. manufacturing industry and encourage job growth, workforce development and equity.
Interestingly, demand for warehouse space in 2023 prevailed at the same time, even during a notably slower period for the industrial real estate market. What this tells us about the current manufacturing mindset is that while we are far from breaking free of the constraints of traditional methods, the demand to embrace digitization and industry 4.0 more broadly and on a commercial level is here to stay.
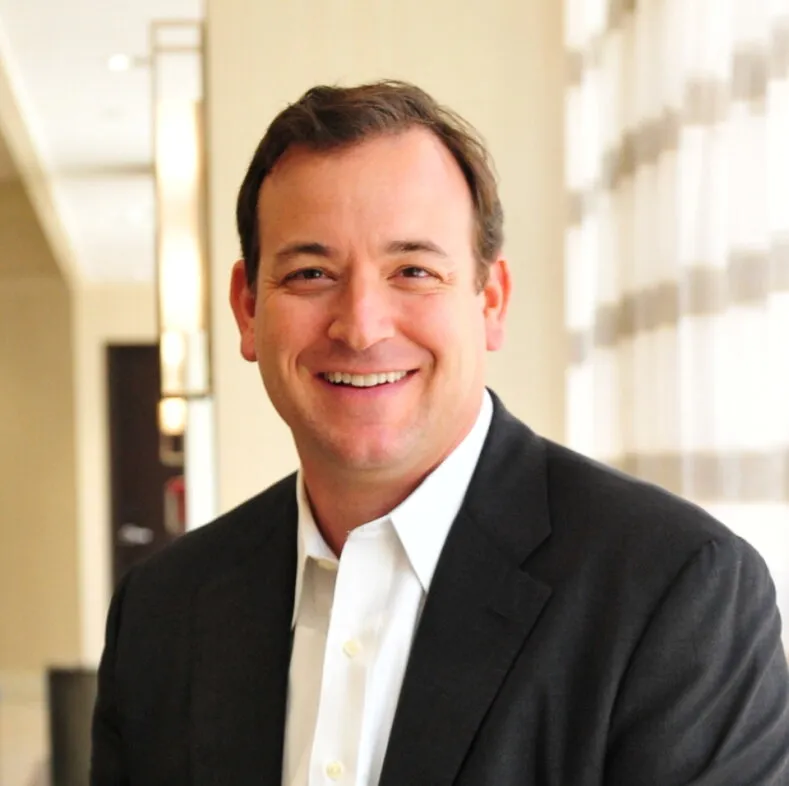
Doing good for business and the planet
Long-term structural investments in technology like additive manufacturing offer manufacturers many opportunities beyond building resiliency into their production lines.
Characteristics like faster development, shorter lead times, less resource-intensive production and highly reusable materials help to reduce waste and minimize carbon footprints. This in turn can help drive innovation in sustainable design, production and distribution. All of which supports manufacturers as they look to make progress against broader sustainability goals in 2024.
Today, manufacturing products with environmental impact in mind from the very start are the foundation of sustainable business. 3D printing is a key enabler of this, whether that’s by creating a circular economy of jewelry and fashion accessories made from 100% precious metals and recycled sources or incorporating recyclability into shoe designs. Even the lightweighting of automotive parts can be used to promote energy efficiency and reduce greenhouse gas emissions.
It is clear that 3D printing is unlocking new design possibilities every day that would be previously unthinkable via traditional manufacturing methods.
Scratching the surface
We are only at the tip of the iceberg when it comes to getting the most out of what 3D printing has to offer from a design perspective. AI and data analytics are poised to disrupt this even further, with 2024 marking a shift from “learning” to “doing.” Even those without design for additive expertise will be able to take advantage of powerful AI models in order to bring designs to life that push the boundaries of innovation, like enabling personalization at mass scale.
Digital tools can help manufacturers simplify workflows to produce personalized goods more quickly and efficiently, advancing customer and patient satisfaction in industries such as healthcare and sporting goods. Further integration with physics simulations will allow manufacturers to predict and optimize printing outcomes without the need for physical printing to take place.
A better control process with a reduction in errors and variation in printed products vastly increases production yield. This will make mass personalization a reality for even more industry verticals, as well as allow additive manufacturing to scale and increasingly challenge traditional injection mold manufacturing.
Scaling to production
Overcoming scalability challenges is critical to the widespread adoption of additive manufacturing technologies in 2024. Fortunately, more and more steps along the additive manufacturing production line are being automated in order to increase production volume while reducing costs and the need for manual labor.
Advancements in these emerging technologies are helping additive manufacturing to integrate seamlessly into smart factory configurations. Soon, digital twins will contribute to an increasingly efficient system that is independent of human intervention through constant analysis, adjustment and optimization of printing processes and parameters, further lowering the total cost of ownership.
It is exciting to think that we are not far off from the reality of “lights out” manufacturing. If we are to make significant progress towards this goal in 2024, we must start leveraging AM as more than just the fortunate stopgap it has been for us to date.