In an industry already plagued by labor constraints, a digital transformation among manufacturers threatens to exacerbate the situation.
The main challenge: a lack of skilled talent. As manufacturers increasingly digitize their operations, workers with more digital skills are required. Since last year, over 500,000 jobs have remained open in the industry, according to a study by Deloitte and The Manufacturing Institute. The study estimates that number will rise to 2.1 million by 2030 if the skills gap continues.
However, more manufacturers are offering programs to up skill and re skill their existing workforce amid the digital transformation. Microsoft’s Chief Technology Officer for Manufacturing Indranil Sircar is working to create programs for manufacturers to accelerate digital adoption and enable them to bring their workforce along.
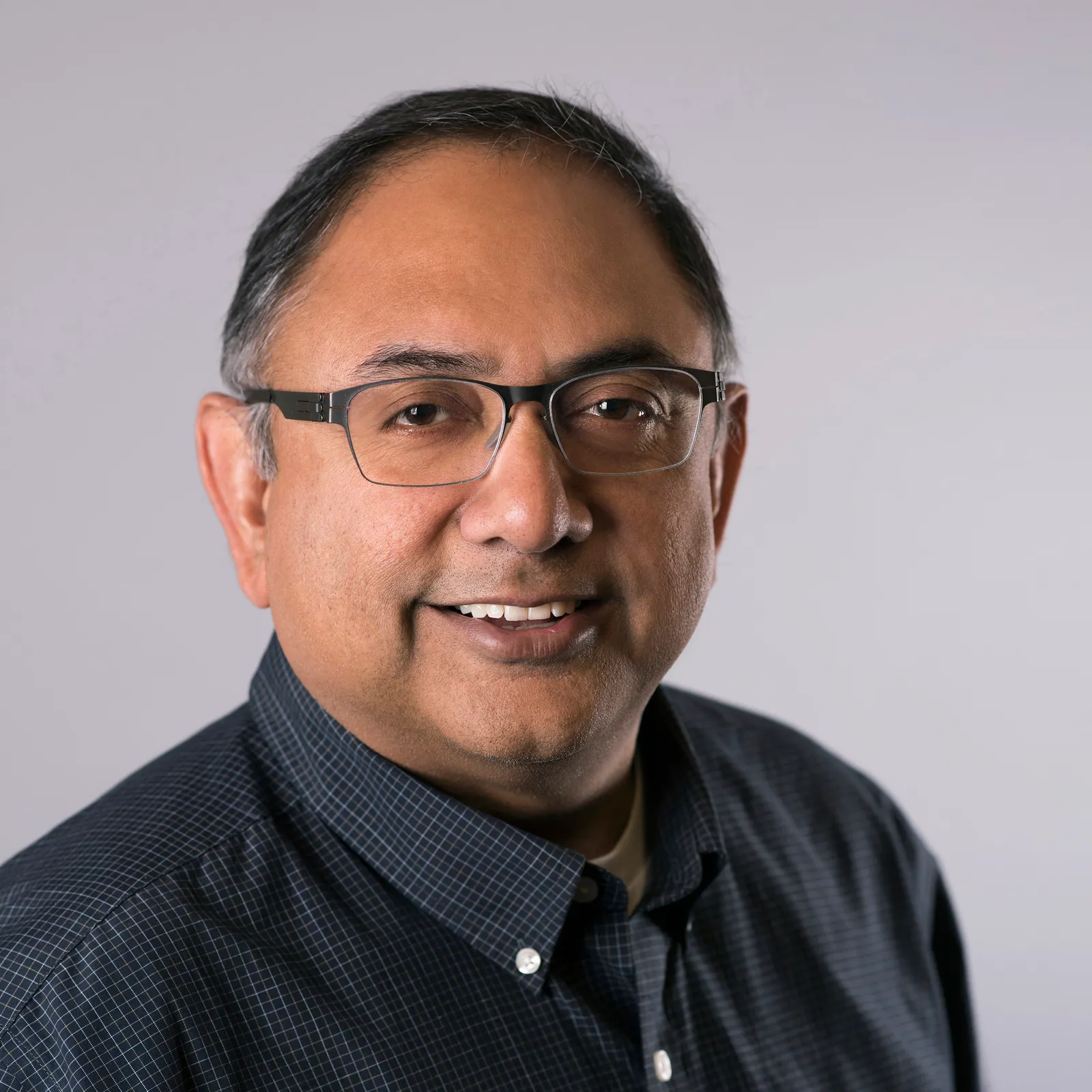
Manufacturing Dive spoke with Sircar about Microsoft’s approach to helping manufacturers digitize, retain their workforces and ensure they have the tools to develop necessary skill sets as the labor shortage continues.
Editor’s note: This interview has been condensed for length and clarity.
MANUFACTURING DIVE: How has Microsoft itself felt the effects of labor constraints in manufacturing?
INDRANIL SIRCAR: Over the years, the industry has evolved quite significantly. A lot of manufacturing processes are outsourced to a great extent, but we still need to manage a lot of that core processes. Whether it’s how we build the product, how we deliver the product, the supply chains and everything else.
The pandemic was one of the early ones when we started to recognize this is something that everybody has faced. We obviously had faced it, but in a different way, mainly because of the way we have structured our supply chain over a period of time. One of the few things that we did was a cultural shift within our own organization. You need to think about the people, you need to think about the talent.
The bigger aspect of it is labor shortages. We are starting to see manufacturing shift more towards the U.S. with the CHIPS Act. We are seeing investments happening in terms of building new fabs and other things in the U.S. The National Association of Manufacturers is predicting significant shortages in the labor area. Microsoft is obviously working with both industries [and] industry forums, with universities and others, essentially trying to see how we can start to help them digitally rethink their manufacturing.
The shift in labor is also about that this is not about the same kind of workforce that existed. These are becoming a lot more people centric, and so, digital knowledge, digital skills, that's where we start to talk about rescaling of the existing workforce because they need to really start to move. So these have been our key focus areas where we have been making significant investment both in our tools, our core capability, working with the industry partners, working with our customer base on how we actually can help them.
Why should companies be focused on up skilling in the current industry climate?
One of the early conversations in the industry was that digitization is going to take jobs away. And what our studies have shown is the reverse. In fact, it has increased employment in a way where the new digital skills just elevates the level of participation of the workforce at a different level. That's been one of the biggest areas of focus in terms of the rescaling aspects of it, although there are repetitive processes.
For example, one of the biggest challenges has been in warehouse management. When things shut down [during the pandemic], how do you actually move materials from one to other? What we're seeing is autonomous vehicles and how they are able to pick and pack equipments and fully automated warehouses are able to do it. Now, that's a level of efficiencies one can gain but you still need somebody to operate them remotely. So those are new skills that have to be built.
What's the biggest challenge that Microsoft has seen companies face when trying to retrain their workforces?
I think it's more cultural than anything else. So top down, we have to work with customers to understand the cultural need for training [and] talent management.
Continuous learning processes, using LinkedIn Learning and other things are becoming a key part of it. So by creating this more inclusive environment – and we practice that ourselves, so for example, our offices on how we think about our workspaces, and work life index and other things that we talked about – they start to play an important role in defining that.
So the challenges are less technical and more cultural – how you actually work. But ultimately, you have to have a very good program also in how you retrain.
What spurred Microsoft to start customizing programs for manufacturers and what do programs typically entail?
We've been coming up with platforms like Viva Connections. It has got a number of different areas: Viva Connect, Viva Insights and other areas from a learning perspective. We have a number of customers who are starting to deploy that and see significant benefits of bringing in that kind of capability. Now, that's more of the connection, how do you actually integrate them into an organization's broader objective of sharing and understanding what their requirements are?
What we're starting to see is very frontline specific, from task management, from scheduling, and then being able to communicate and collaborate. One of the biggest things about manufacturing is how do you actually manage the knowledge aspect of it? Are we able to bring together some of those knowledge or problem solving capabilities together?
As an example of it, the [Microsoft] Teams collaboration capability with [our] frontline workers cues – which are more manageable, much more smaller – allows for worker onboarding and [simple] things like push to talk.
Then, moving to a more manufacturing focused use cases. That’s where we work with partners: Spartan vendors and others on Gemba Walk, or quality management on how you do virtual Kanban processes.
The third level is creating a mixed-reality-based capability, which we start to see using HoloLens in our mixed reality guides. [It’s] essentially allowing much faster way of how you train the people on the job. We have a number of our customers like Toyota and others who have been using it effectively in keeping their people up to speed.
So how have Microsoft systems helped to speed the process of up skilling workers?
It is the programmatic way how we look at it from the onboarding of workers. Getting them to adopt the tools much faster. Giving them the right tools at the right place. But again, platforms will generate capability, but ultimately there has to be change management programs that allow these things to happen within an environment.
We build tools that are capabilities and platforms that enable everybody to collaborate and be flexible enough to build a kind of process.