Jason Waxman is president of Fluke Corp., a wholly owned subsidiary of Fortive Corp., and a world leader in the manufacture, distribution and service of electronic test tools and software. Opinions are the author’s own.
As we begin 2025, let’s take a moment to review the current industrial landscape.
While there are always short-term fluctuations based on regional economies, I prefer to look at the macro trends shaping the industry and how they are impacting what we and our customers do. It’s clear that we are at a convergence of technology and sustainability, which is reshaping the future of the manufacturing sector.
As we navigate a complex web of challenges and opportunities, it often feels conflicting on where to focus our efforts. Assessing the drivers of these changes is a good place to start, then looking at what needs to be done to encourage stability and lastly devising a clear strategy for change that is appropriate for your business.
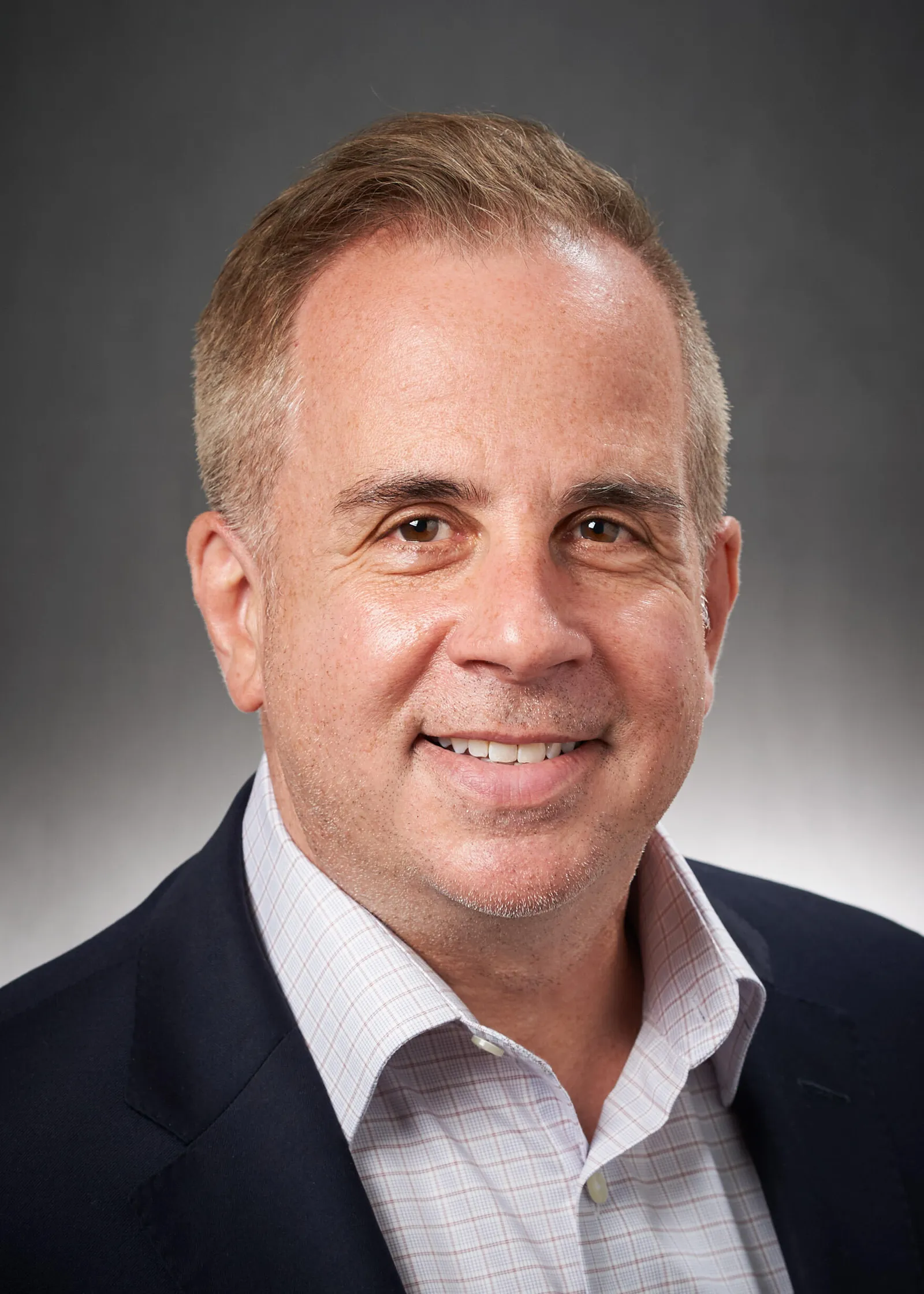
Grid modernization: propelling clean energy forward
The first driver of change is the surge in demand for renewable energy, driven by community initiatives and government incentives aimed at achieving net-zero emissions, bringing both significant promises and of course, hurdles. The rapid expansion of renewable energy sources driven by community initiatives, such as solar power and electric vehicles, necessitates a robust and reliable infrastructure. This requires not only advanced technology, but meticulous attention to safety and comprehensive training programs.
Grid modernization is crucial for the successful integration of renewable energy sources. We’re at a critical juncture — much of the United States' solar capacity is nearing the end of its operational life. The Department of Energy notes that 70% of U.S. transmission lines are over 25 years old. This challenge presents a significant barrier to integrating renewable sources.
We need to modernize our aging infrastructure to support the growth of the industry. These efforts involve routine maintenance and upgrading key components to enhance efficiency and longevity. This is obviously a significant investment, but a worthy one.
Advanced tools and technologies, from diagnostics to repairs, are needed to facilitate this transformation. Willie Phillips, chair of the Federal Energy Regulatory Commission, said it perfectly during a May news conference, "Our grid is at a make-or-break moment.”
Enhancing EV charging infrastructure
Also related to the recent surge in focus on electrification, the reliability of EV charging infrastructure is a critical factor influencing wider adoption of EVs. A recent study from the Lawrence Berkeley National Laboratory shows that nearly 2,600 gigawatts of new electric capacity, including wind, solar and storage, are waiting to connect to the grid.
However, charging station malfunctions are a concerning trend. The National Renewable Energy Laboratory estimates that the U.S. will need about 28 million charging ports by 2030 to meet the demand for zero-emission passenger vehicles.
To ensure these essential services keep pace with growing demand, meticulous maintenance and advanced testing and measurement tools are essential. Public and private charging networks must be reliable and efficient to build consumer confidence in electric mobility.
As of December 2024, there were 10,688 unavailable EV chargers, which does little to reassure the wider population that we can cater to growing demands where needed.
What do we need to succeed? Above all, a workforce with the capacity, training and skills needed to install and maintain this industry as it grows exponentially. But more than that, we also need a better way to commission the capacity, sufficient standards around maintenance and calibration of chargers, and the right tools to support technicians in the field.
To truly support the electrification of the world, the focus on safety and training must remain a top priority. By establishing stringent safety and maintenance standards and investing in comprehensive training programs, we can ensure that our workforce is well prepared to navigate the complexities of renewable technologies. This not only protects workers but also enhances the overall efficiency and reliability of the renewable energy sector, supporting growth into the future.
Revolutionizing manufacturing through AI and automation
The promise of artificial intelligence in manufacturing continues to expand to new use cases, and with it hopes to close the growing skills gap that threatens the output of the industry in the near future.
According to a recent Fluke Reliability AI report, manufacturers are investing, on average, 44% of their technology budget on AI. In addition to boosting productivity and efficiency, respondents confirmed their organizations are using AI to optimize supply chains (28%), enable enhanced decision-making (27%) and bridge the skills gap created by the ongoing skilled labor shortage (31%).
However, we may be in the early stages of the hype curve with much experimentation, but not as much clear return on investment.
One area where I've seen true AI impact is in predictive maintenance, which can anticipate machine issues up to six months prior to occurrence. This is game-changing for businesses, as it means they can plan the most suitable time for the work to happen, plus, they can ensure they have the correct inventory and workforce resources on hand. This will have an enormous impact on the bottom line of most manufacturers, with unplanned downtime currently costing millions.
A strategic embrace of AI and automation is a step in the right direction to address chronic labor shortages and enhance workforce skills, contributing to a more innovative work environment.
Solving workforce shortages with innovative technologies
With the shortage of workers expected to reach 1.9 million by 2033, we are in a race against time to take the correct course of action.
How do we get there? While many touted AI as taking the jobs of individuals, I challenge a different perspective. What if it takes the burden away from mundane tasks, freeing up the workforce to do the skilled labor that requires more in-depth attention?
With automation and AI technology at our fingertips those that are investing and implementing the technology now will have the chance to find the balance of man and machine. We recommend always prioritizing a human-led approach.
While some businesses are struggling with where to start, The World Economic Forum's collaboration with the Boston Consulting Group on the AI-powered Industrial Operations initiative aims to support manufacturers in capturing the full potential of AI.
This initiative focuses on raising awareness of AI applications, as well as developing an educational guidebook for implementing and scaling AI in industrial operations. As Jay Lee, founding director of the Industrial AI Center at the University of Cincinnati, asserts, "AI should not be a trial and error — it should follow a systematic approach."
Navigating the path forward
It is critical that companies support essential workers through these transformations with foresight and responsibility. Embracing modernization, prioritizing reliability, leveraging technology and ensuring safety and training are paramount. By focusing on accuracy in testing and measurement, maintaining robust infrastructures and investing in our workforce, we can create a resilient, sustainable and innovative future.
The integration of renewable energy sources and the modernization of our industrial operations are not just technological challenges—they are opportunities to redefine our future. By overcoming these challenges and harnessing the opportunities, we can drive progress and innovation for generations to come.