Ion Storage Systems launched its pilot line and opened its solid-state battery facility in Beltsville, Maryland, on Monday.
The 33,000-square-foot facility currently has 75 employees and is expected to increase to 150 over the next three years, the company said in an email to Manufacturing Dive. The pilot line, dubbed “Megapede,” has a capacity of 1-megawatt hour a year, with plans to increase it to 10 MWh, executives said.
“Further expansion is currently being planned but we cannot disclose the details or locations we’re considering at this time,” the company said in the email.
Nonflammable materials
Solid-state batteries are made up of carbon, titanates, lithium alloys and metallic lithium. These batteries can charge faster and last longer than nickel manganese cobalt and lithium iron phosphate batteries, according to a study published in Nature Materials in January.
Solid state batteries are also safer, Robert Whittlesey, principal technical program manager at Ion Storage Systems, told Manufacturing Dive in an interview. Lithium-ion batteries have a flammable liquid electrolyte, which can ignite fires if not handled properly.
Instead, ISS exchanges the flammable materials for a non-flammable component, ceramic.
“You get all of the performance benefits of lithium-ion batteries,” Whittlesey said. “And so it's kind of like a no-duh in the sense that we can really revolutionize how we store energy and make it safer.”
ISS is working with chemical maker Saint-Gobain, which produces the ceramic powder for the battery maker’s electrolytes, Neil Ovadia, VP, supply chain, told Manufacturing Dive.
“Imagine a ceramic plate,” Ovadia said. “You can stick it in the oven, you can stick in the microwave, nothing will happen to it, and it's also inexpensive. It uses materials that are regularly available.”
Furthermore, the startup is working on how to recycle its batteries.
“Basically you can take old pieces of ceramic, process them and get as good as new virgin material,” Whittlesey said. “And so that's something that is still in progress, but the idea that you have a fully recycled battery is kind of mind-blowing and really exciting.”
‘Crawl, walk, run approach’
The company is working with the U.S. Army to domestically produce conformal wearable batteries, which soldiers can use for portable electronic gear such as radios in the field.
In August 2020, ISS received a $2 million contract from the Defense Logistics Agency to modify the conformal wearable battery, which it expects to deliver later this year, Board Director and CEO Ricky Hanna said in an interview with Manufacturing Dive.
But that’s ISS first market product, Hanna added.
In addition to the military, ISS is working with 40 other companies in the consumer electronics, electric vehicle and grid energy storage industries.
“We're going to give them hundreds of batteries to test, prove to them that our technology works and it's non-flammable, and it's more energy,” Hanna said. “And once they see that, that's going to lead to commercial agreements.”
Still, the startup is taking a crawl, walk, and run approach to these industries due to cost sensitivity and low volume, Hanna said.
“We [will] get in once we're more mature and we have our yields and our supply chain under control,” Hanna said. “Then we venture in 2028 into EV and beyond that, then we go into grid energy storage.”
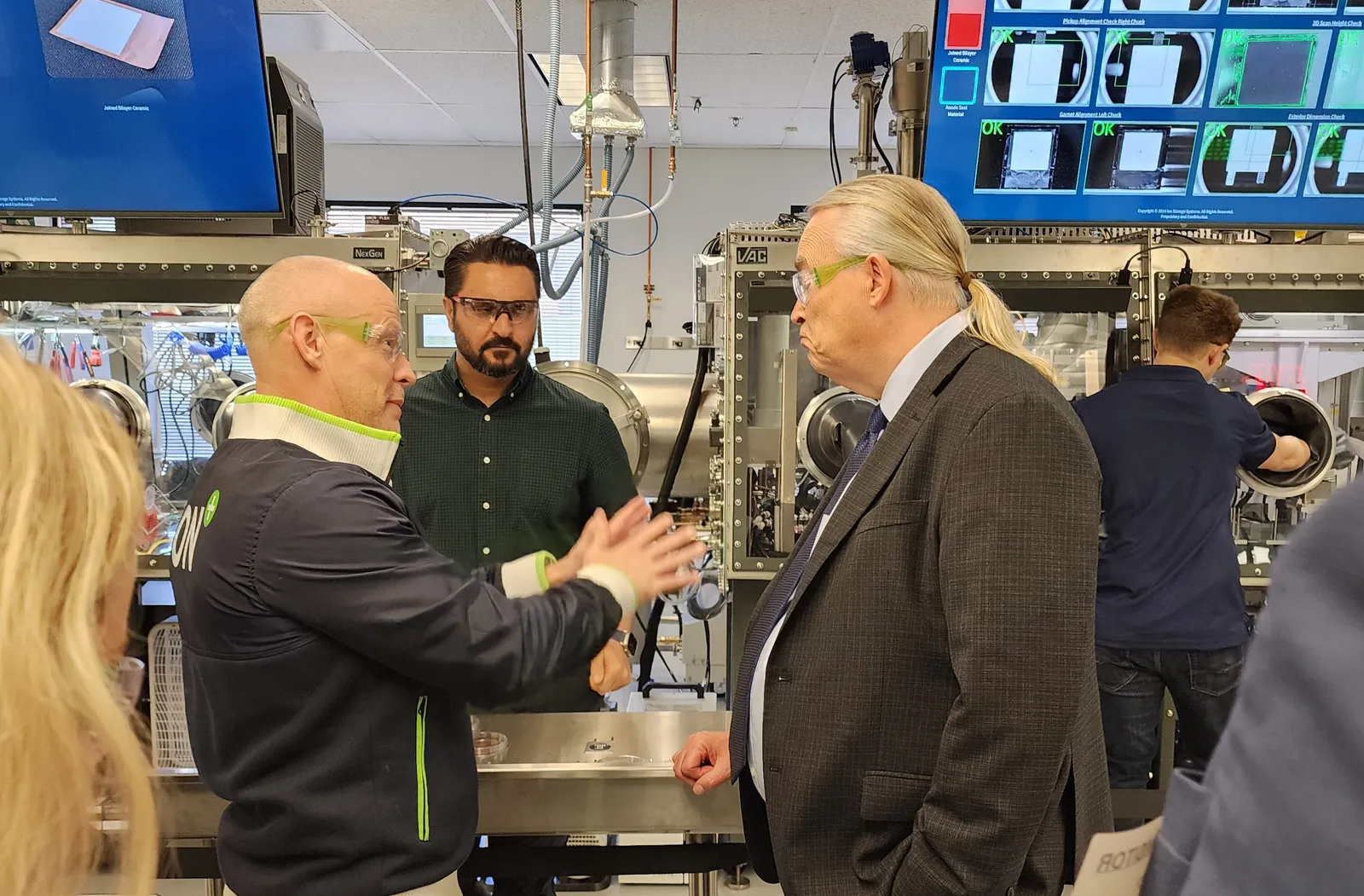
The materials will also be domestically produced in the U.S. and will have no cobalt or nickel.
“We've got a very good domestic supply chain established in the U.S.,” Ovadia said. “And the complexity that's required from a lithium-ion standpoint, in an electric vehicle, for instance, to keep it cool to warm it up before charging, that goes away with our battery because we don't require all that complexity.”
While the manufacturer is using nickel, manganese and cobalt for its first-generation product for the Army, the next generation will not have these materials due to China’s domination of critical minerals, rising costs and the country’s exploitation of slave and child labor in the Democratic Republic of Congo, Hanna said.
ISS chose Beltsville because it’s near one of its partners, the University of Maryland, where the startup spun off from the school’s Maryland Energy Innovation Institute. Years before the company was established, the Department of Energy first funded UMD’s solid-state battery project in 2017 with approximately $5 million through the agency’s Advanced Research Projects Agency-Energy, which funds energy projects in their early stages.
ARPA-E funded the university again in April 2023 with $4.8 million under its EVs4All program, which will help the school and ISS work on improving the process and make it cost-effective.