The majority of U.S. manufacturing firms are quite small. In 2021, roughly 98% of U.S. manufacturers had less than 500 employees, according to the National Association of Manufacturers, and three-quarters of firms had fewer than 20 employees.
The cost of federal regulation compliance, including Occupational Safety and Health Administration standards, falls disproportionately on smaller manufacturers, according to NAM.
Manufacturers pay $29,100 on average per employee to comply with federal regulations, nearly double the $12,800 per employee costs borne by all firms as a whole, according to a NAM October 2023 study. The burden is even greater for manufacturers with fewer than 50 employees, which incur the highest regulatory costs of all U.S. firms — an estimated $50,100 per employee per year.
Given these higher costs, it is particularly important for small manufacturers to remain compliant with federal safety regulations to avoid strenuous penalty fees.
Applying the right OSHA standards
OSHA issued 29,590 citations in fiscal year 2023. The top ten violations in 2023 included fall protection, hazard communication, ladders, scaffolding and powered industrial trucks. Other top violations include respiratory protection, lockout and tagout and personal protective equipment.
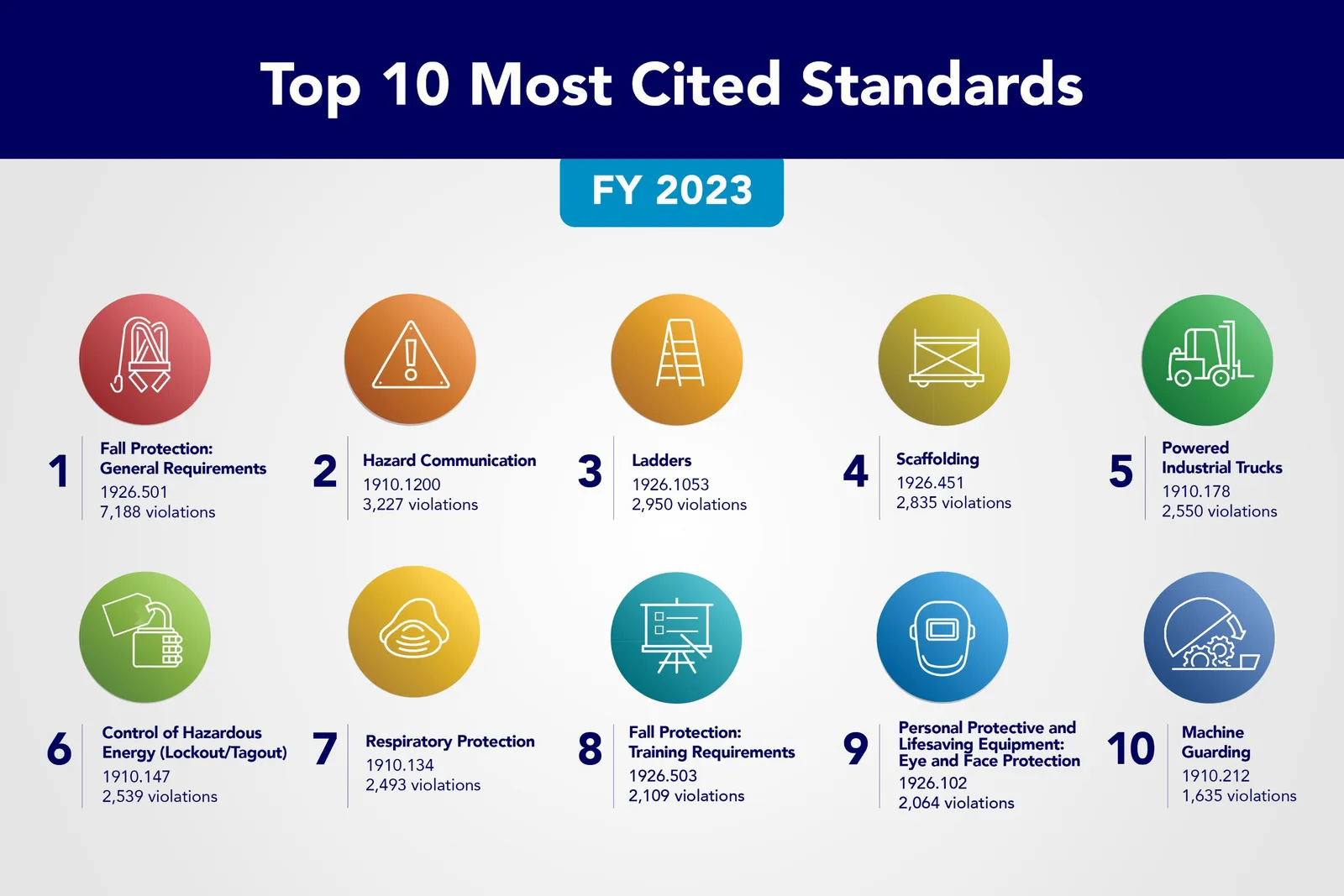
For insights on handling OSHA inspections and staying compliant with safety and hazard laws, Shannon Dennis, the national account manager at Safety Consultants USA, spoke on a panel at the 2024 Women in Manufacturing Conference earlier this month.
A good first step in safety compliance is knowinf what OSHA standards apply to the firm, Dennis said. For the manufacturing industry, standard 1910 is a set of general industry safety and health guidelines, such as fall protection and hazard materials handling. For more construction-specific standards, 1926 is more industry-focused.
“What is OSHA law going to tell us? It's going to tell us what type of injuries you're having in your facility. And a lot of times, what we see is people that are overreporting or underreporting. So you want to make sure you have the knowledge,” Dennis said.
Be ready for a visit
It's also important to know why OSHA could make a factory visit. It could be due to an in-patient hospitalization, amputation or eye loss, which employers must report to OSHA within eight hours, or a fatality, which must be reported within eight hours.
The facility could also have had an employee complaint, national or local emphasis programs, or is undergoing a scheduled OSHA inspection.
Once OSHA arrives at a plant, factory management should follow a set protocol to ensure their manufacturing team is ready to greet officials.
“Larger corporations typically seem to have more layers of legal counsel, and it may be that the policy is to not let them in and have them come back in the morning,” Dennis said. “For most of our smaller manufacturers, we want you to cooperate with them, but have a plan. And you want to have your gatekeepers and you can train them what to do.”
Dennis advises that the employees at the front of the office understand how to greet OSHA, and ensure the highest-ranking person at the facility escorts them and gives them only documentation related to the incident they are investigating.
“If you have near misses or incident reporting, you want to do a root cause analysis, or at least use that information to try to determine, ‘How do we prevent this from happening? How do we prevent this from becoming an actual injury?’”

Shannon Dennis
National Account Manager at Safety Consultants USA
As for preventing accidents, maintaining record keeping of occupational injury and illness records is vital. A company is required to have three years of OSHA record logs accessible, though Dennis recommends having five years of data that’s updated regularly.
It’s key to create a comprehensive safety manual of policies and programs, as well as perform hazard assessments, inspections and audits on an ongoing basis, Dennis added.
“You want to have corrective actions in place for your negative findings, and knowing what you can do with that information,” she said. “If you have near misses or incident reporting, you want to do a root cause analysis, or at least use that information to try to determine, ‘How do we prevent this from happening? How do we prevent this from becoming an actual injury?’”
OSHA offers a no-cost, confidential on-site consultation program tailored primarily for smaller businesses, an OSHA spokesperson said in an email to Manufacturing Dive. This program assists employers in identifying hazards, improving safety and health programs and ensuring a safer work environment — without the worry of penalties or fines.
How one small manufacturer tackles safety
Maine-based Cotton swab manufacturer Puritan Medical Products formalized its safety programs once the company expanded its factory network, which now includes three locations. The program includes systems such as emergency response teams, first response plans and defined
“We developed. . . first response plans, so that there's defined [standard operating procedures] for how to respond to different things, natural disasters, injuries on equipment, things like that,” said Site Director Troy Lord. “We formalized a lot of it. We formalized responsibility, annual training.”
The company also emphasized the importance of having employees feel comfortable to speak up on safety issues, even to the executive level.
To help create that culture, manufacturers should train employees on site-specific programs and policies and develop a trackable training matrix so that all safety procedures are documented, Dennis said.
Dennis said that while some training can be conducted online, hands-on instruction is better for certain tasks, like lockout and forklift training.
“Forklift training required the hands-on component. We have to take people out, let them operate the equipment and evaluate their use of that and document that portion as well, separately from written tests,” Dennis said. "Also with the in-person training, it gives you a really good way to assess that person's knowledge.”
Kate Magill contributed to this report.