In recent years, tech giants including Google and Microsoft have ventured into the manufacturing space, putting out AI platforms and visibility tools specialized for manufacturers and supply chain professionals.
The products are part of a broader push in the industry to use AI to enhance operations, including better demand forecasting and more seamless product supply chain from assembly to delivery. Integrating such tools can present a challenge however, as companies navigate how to properly analyze and apple the trove of data these tools can collect.
Manufacturing Dive recently spoke with Google Cloud’s Director of Manufacturing and Transportation Industries Simon Floyd about the company’s foray into in the industry, and what he sees as areas of opportunity for manufacturers to better integrate AI into their daily operations.
Editor’s note: This interview has been edited for clarity and brevity.
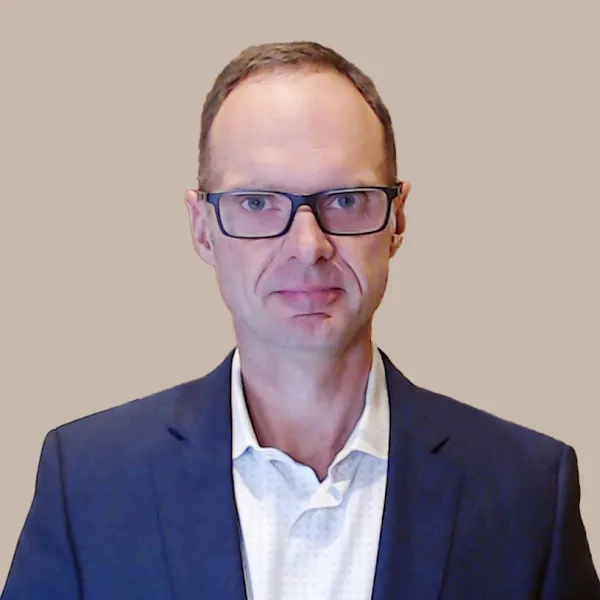
MANUFACTURING DIVE: On an industry-wide level, are there any particular tech developments right now that are proving really helpful for manufacturers?
SIMON FLOYD: The adoption of big data technology has made a really big difference for manufacturers. But I think that really the next wave [of development] is helping them understand how to derive more value from the data that they're now managing.
And one of the newer technologies that we just brought to market is our Timeseries Insights. And one of the reasons why is it takes a lot of the complication of data science and it just unloads it into the application. So that you don't have to do it, instead [the] AI actually does that for you.
I think it's a fantastic example of where AI actually helps you because it does the difficult work and gives you the results you want. That's really what manufacturers are looking for. They want to get down to the results. And they want to do that in a way that's going to be repeatable.
In a manufacturing operation, what are some of the tasks that big data can be used for?
FLOYD: This is a great question about industry maturity, and where they are on their digital transformation journey. The current state of where we are as an industry is in the monitoring and data collection stage. Most manufacturers know where they want to go, to be able to use that information to help them with a range of use cases which are fundamental to how the operations work.
And that begins with better forecasting. It begins with just having better manufacturing planning. It goes through to how the factory is actually performing, making sure that the equipment is always available for that manufacturing order of the day. There’s an unlimited amount of capacity for this manufacturing organization that runs effectively through the entire product lifecycle.
How can data help manufacturers and their supply chain operations?
FLOYD: For me, this is about visibility. We have a solution called Supply Chain Twin, in which it does exactly that, it replicates the real world in a digital world. You've got visibility into what is inbound into the factory, what is outbound from the factory. And when we combine it with our manufacturing data engine, then that gives you visibility of the supply chain through the factory.
So we've got three strong components. There's the demand side — what you need to get from your supply chain. What happens when it's being produced through your factory, and then what happens when it goes out to warehouse, out to logistics, or directly to the customer. The visibility is very important.
We apply artificial intelligence here as well, so that we've got a more forward-looking understanding of the supply chain, which is really critical for planning. You want that understanding of what could occur over the next three months, maybe the next 12 months, so that you can make an accurate plan.
Are there any opportunities you think are particularly untapped among manufacturers to integrate these types of tools?
FLOYD: We as an industry are still very much in that data collection phase. And part of the challenge that many manufacturers have is that they have a lot of siloed systems, which they’ve got through acquisition, as an example, or just of buying best of breed or best of class over many years. And it makes it difficult for them to get the insights that they're really looking for.
The opportunity is to turn that information into intelligence for the business. I've spoken to so many manufacturers who just have a really difficult time with the forecast. Quite often what they do is just to repeat what happened last year, and it’s not the smartest way to go about it.
That is the new step forward in that maturity model, is to go to the information they have and turn it into new insights or intelligence to drive the business forward.
When it comes to the people who can turn that data into something useful, do you see that a lot of companies, especially smaller ones, have the staff to do so or do they need to hire individuals with these skills?
FLOYD: I haven't really seen a circumstance where it's any difference in a small organization as it is to medium size or a bigger organization. Sometimes I think it's got a lot more to do with the way that organizations are hiring. So, maybe sometimes smaller organization, they might be hiring brand new graduates that are coming into the organization that have data science skills, that's why they are seeking a career in manufacturing.
And then on the other side of it, I've seen very large organizations where they're upskilling the workforce that they already have and then teaching them new skills. I would say that for organizations that are more traditional and established, the concept of data science is a new skill that they're looking to acquire.
For some of the younger manufacturers, say the ones that may be in the electric vehicle space, it's a really easy one to get their arms around because they are effectively brand new . . . It's just what they knew they needed to have from the start.
Are there any other challenges that companies should be aware of when looking to integrate AI tools?
FLOYD: There is still that gap between the information tech side of the house, traditional IT, and the operational tech side, which is your OT. The difference between the two worlds is still there. That unto itself is an integration opportunity that will help them get more of those data-driven use cases under control.
When I think back on where we came from as an industry, it was not an intentional design that those two worlds would be different. It was never an intentional design to have all these silos. It was just part of the evolution. And now we are at that point where convergence is now mission critical.
Because in very simple terms, the opportunity to understand what occurs in the factory, we have that, that's baseline monitoring. But the part of the organization or enterprise that is normally in the IT world doesn't have access or visibility to that information in an easy way.
So really combining the two of them is the smart move for a manufacturer. The bigger challenge for manufacturers is overcoming the gap that they have between those two parts of the organization and getting them to have a single digital strategy.