Before Hurricane Sandy, the idea of flooding seemed a distant prospect for many communities outside of flood zones. Today, following an autumn that saw major hurricanes destroy factories and businesses, that risk seems to have crossed the threshold into a more immediate possibility.
“There is no such thing as ‘low risk’ or ‘high risk,’” said Firas Saleh, a director of product management at Moody's. “Where it could rain, it could flood. It’s very simple.”
The physical risk presents a clear financial one as well. According to the Federal Emergency Management Agency, “just one inch of floodwater can cause up to $25,000 in damage.”
On the other hand, understanding how a manufacturer can assess their risk and take measures to protect workers and factories isn’t as straightforward.
Understand and mitigate major flood risk
Manufacturers can use flood mapping and risk assessment tools, including those from Climate Mapping for Resilience and Adaptation, the National Oceanic and Atmospheric Administration and Argonne National Laboratory, to better understand their geographic and climate vulnerabilities.
The tools can help manufacturers differentiate the different types of flooding their facilities could be prone to, including fluvial flooding — flooding that occurs when a river floods over its banks — coastal flooding and pluvial, or rainfall, flooding.
Once companies fully understand their risk, they must choose how to mitigate the possibility of a flood, including how much to invest.
Manufacturers who are ready to commit to comprehensive flood mitigation measures might want to consider “wet floodproofing,” or floodproofing that accepts that portions of a factory or office building might come into contact with water.
Often used to protect non-critical areas such as parking or storage, wet floodproofing involves tactics like using flood-resistant finish materials that are “easy to clean and can withstand prolonged contact with floodwaters,” says FEA Facility Management Consultant Stephen Meador.
“Openings or breakaway walls” might also help floodwaters enter a structure in a controlled manner.
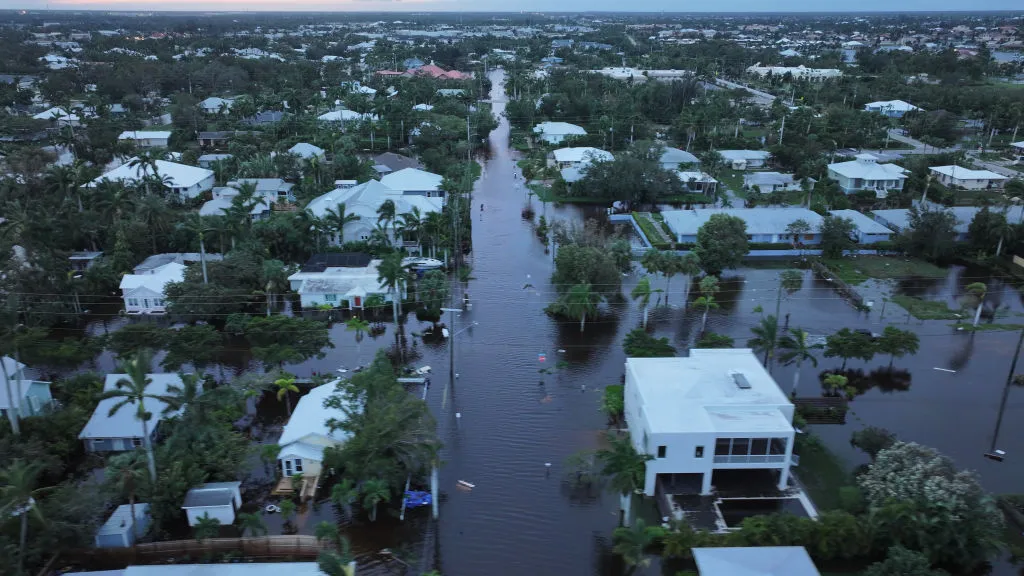
To secure more mission-critical parts of a facility, however, manufacturers will want to invest in “dry floodproofing,” or efforts that attempt to keep water from ever coming into contact with a building.
“Measures involve making the structure resistant to flood loads and making the building and utilities watertight using fixed measures such as door and window barriers, flood walls, NEMA submersible enclosures,” said Meador. “This can be a challenge because both dynamic and static forces can become tremendous as floodwaters are flowing and rising.”
Other temporary dry floodproofing measures include sandbags, water-absorbing deployable barriers, and numerous types of portable, modular, reusable barriers that utilize the weight of the water to hold them in place, according to Meador.
The effectiveness of these investments can’t be discounted: In the lead up to Hurricane Milton’s landfall, Tampa General Hospital in Florida installed water-impermeable barriers that prevented flooding and kept the lights on.
Many businesses keep these structures close at hand. According to Elwell, one JLL airport client maintains ready-to-build flood gates that can take up to seven days to put together. While expensive and requiring multiple personnel to deploy, such tools can mean the difference between business-as-usual and thousands of dollars in replacement and recovery costs.
Flood mitigation measures don’t have to stop at prevention. Backflow prevention devices can also help get water out quickly, and pumps and generators can ensure a power supply, says JLL President of Industrials Division Meaghan Elwell.
'Quick wins" to make a facility flood-resilient
For business owners who aren’t in a position to make large investments in flood mitigation measures, there are some “quick wins” available to most budgets, said JLL President of Industrials Division Meaghan Elwell.
Initiatives include elevating key pieces of equipment from a basement mechanical room to higher elevation, or simply creating a business continuity plan in case of a weather disaster. For the latter, Elwell advises identifying vulnerable parts of the building and important equipment and outlining clear communication channels, beyond cell phones and radios.
“And then, of course, think about, ‘How does business go on?’ That is the definition of business continuity. To the extent that your operations can continue, how do you ensure that you’ve thought through access into the network through VPNs?” Elwell said.
Senior VP of Global HDD Assembly and Backend Operations Philip Bernard at Western Digital, an international manufacturer of hard disk drives that successfully weathered severe flooding in Thailand in 2013, adds that ensuring a company’s leadership “is involved and takes ownership in the process,” is important to preparing for flood risk.
That process involves not only conducting an annual “physical climate vulnerability analysis” to assess the risks of physical climate at each of its manufacturing sites,” but also organizing a business continuity management risk assessment that reviews procedures on a yearly basis, said Bernard.
Insuring against flood risk
Of course, one can’t think of flood protection without considering flood insurance.
A flood insurance policy is not typically included in commercial property insurance and must be purchased separately, said Moody’s Saleh.
Manufacturers can either choose between private flood insurance or the National Flood Insurance Program. While rates will vary depending on location and needs, NFIP flood insurance can cover up to $500,000 in building damage and $500,000 in contents damage.
Both building and content coverage are usually purchased separately and maintain different deductibles. NFIP flood insurance, with few exceptions, goes into effect a full 30 days after purchase.
Alternatively, private insurance options offer flexibility in the waiting period, deductibles and coverage limits.
To make the best decision on insurance providers, Saleh said manufacturers should consider several key factors.
First, specifically when it comes to choosing a private provider, businesses should make sure their insurers have excellent financial credibility.
“Look at the financial health of these insurance companies, look at their historical track record. We’ve seen cases where some of these insurers could not meet [claim] applications after mega catastrophic events,” Saleh said. “After Hurricane Andrew in 1992, many carriers went insolvent because they didn’t have enough to cover [claims].”
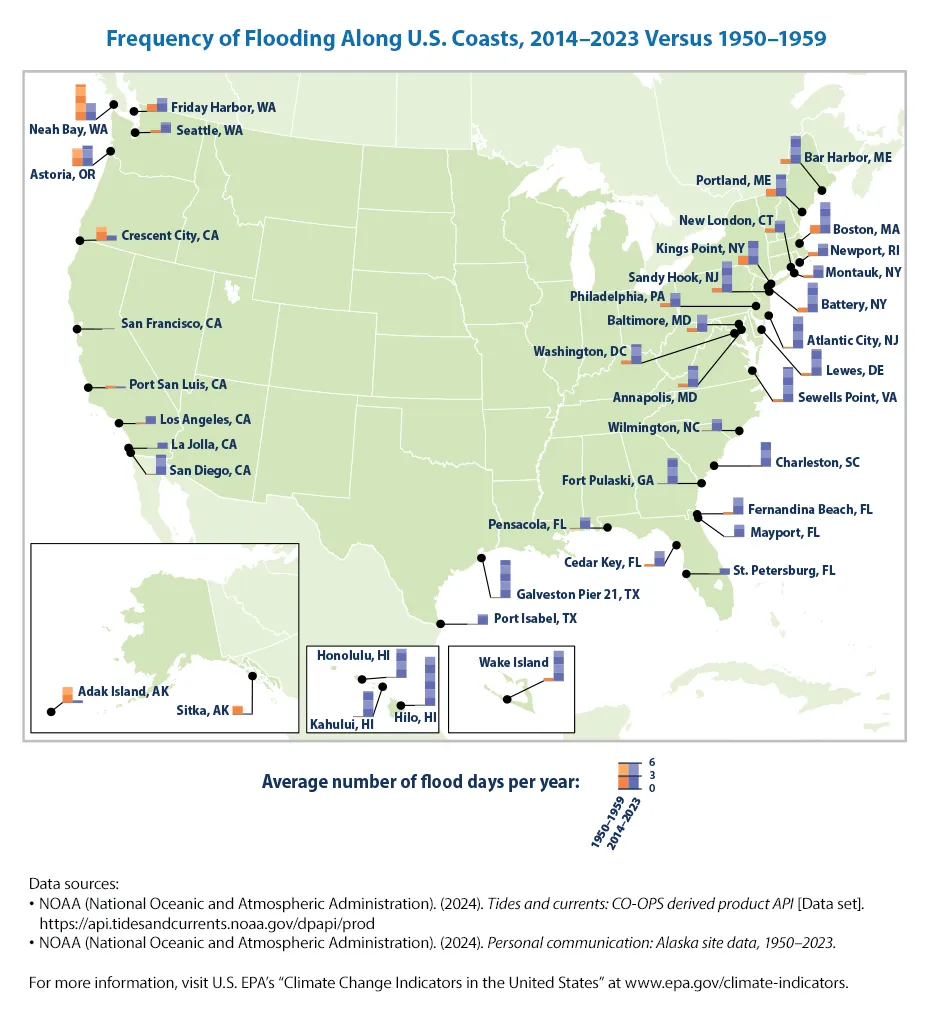
Then, do homework on exactly how much coverage a company might need.
“Flood insurance doesn't mean you’re fully covered, because of the issue of sub limits,” Saleh said, referring to the $500,000 limits on both content and structural coverage. “So you could possibly have flood insurance, but you could be underinsured. And that is the challenge.”
Better yet, find out exactly what qualifies as flood damage. According to FEMA, “if rain is propelled into a covered structure by wind, that is considered wind-driven rain and is not covered under your flood insurance policy.” In the case of flood insurance, nuances matter.
And finally, it would be wise to investigate exactly the type of payout that would be offered in case a claim is filed.
“There could be a big difference — when you get the claim payout — between the replacement value and the actual cash value,” Saleh said.
How to expect the unexpected
Various innovations in monitoring systems can help manufacturers prepare for flooding.
“When Sandy hit 12 years ago, we had some forecasts that [let us know,] Ok, we have a storm forming in the New York-New Jersey area, but we didn’t have the level of predictions that allow us to say, You could expect up to six to eight feet of water on this specific property. Now we have those capabilities,” Saleh said.
Case in point: At Western Digital, facilities are equipped with water level monitoring systems that monitor “real-time water levels and manufacturing sites in Thailand,” said Bernard.
Such tools can also pair well with supply chain risk assessment systems that provide real-time visibility into suppliers' status and response. Additionally, manufacturers can use 24/7 communication mobile apps that can check-in to signal whether a team member is safe or deploy resources to address disruptions, added Bernard.
“Our best advice would be to ensure your company’s leadership team is involved to take ownership in the process and lead by example." Bernard said. "Implement programs for flood hazard modeling, resource protection and preparation. Ensure you are performing risk assessment studies and implement business continuity planning."
Correction: An earlier version of this story misspelled Moody’s Director of Project Management Firas Saleh’s last name in some instances. It has been updated to include the correct spelling.