In October, Italy-based solar panel manufacturer Enel announced plans to open its first factory in the U.S. The factory, produced with Enel’s affiliate 3Sun USA, is expected to produce up to six gigawatts of photovoltaic (PV) solar panels per year, making it one of the largest facilities of its kind in the country, according to a company press release.
Enel is currently evaluating possible site locations, with construction expected to begin in mid-2023. The factory will be Enel’s second, in addition to its first factory in Italy.
The move comes as more companies are pushing into sustainable manufacturing to take advantage of new incentives offered by the Inflation Reduction Act and the demand it is set to spur.
Manufacturing Dive talked with Giovanni Bertolino, head of 3Sun USA, Enel North America about the company’s push into solar power manufacturing in the U.S., including what it’s looking for in a potential site and how it plans to support the facility with a strong talent pool and supply chain.
Editor’s note: This interview has been condensed for length and clarity.
MANUFACTURING DIVE: Can you give an overview of the major facets of the upcoming plant that's being planned for the U.S.?
GIOVANNI BERTOLINO: We are planning to deliver a factory that will produce PV cells and PV modules, and sell those in the United States to serve the needs of both utilities when they are deploying large scale solar plants and also [to]. . . residential and commercial [customers] when installing panels on the roof. The two products are slightly different in terms of final assembly, but the core cells will be the same.
It's been mentioned that the new plant will employ up to 1,500 new roles. What are some of those positions and how do you plan to source and recruit those different positions?
That's one of the biggest challenges that we are looking at when selecting the site. We’re going to be completing our site selection and having access to the right talent pool and labor availability will be a key factor. So, 1,500 [people] is what we are estimating for when we're going to reach 6GB of solar panel annual production.
The majority of those roles will be in the actual manufacturing side. This will be a highly automated factory, a smart factory, because we have the application of automatization, software controls, digital intelligence monitoring the line, optimizing and finetuning the manufacturing process. All these key elements that are needed to manufacture the cells. You know there are a number of chemical steps that go into the process and then the assembly line for the modules are competencies . . . that requires a deep understanding of what is happening in order to be able to control and ensure that they are functioning to their potential.
Are you thinking of being near universities or training centers? Are these roles you plan to internally train?
I think we will mostly train internally, of course leveraging, the support that the local workforce development center can provide. What we're going to deliver here in the United States is a sister facility to the one that we have in Italy that is expanding. We've done a bit of leveraging the learning curves and experience in setting up a factory in Italy.
So we will have people going to Italy as we ramp up the factory there, which will start preparations about one year before the one in the U.S., and then come back here exporting their learnings and train the trainees here.
The talent pool that we are looking for will be mostly coming out of vocational schools, colleges or maybe even directly from high school. People who have a passion for the renewable space, of course, technology and are willing to learn and grow in a manufacturing environment. We also need engineers. For the site location, having a good university is a plus, but we're mostly looking at the location where there's a stronger college or vocational system of schools and good access to labor. Locations that we're looking at are reasonably close to large cities in the Midwest.
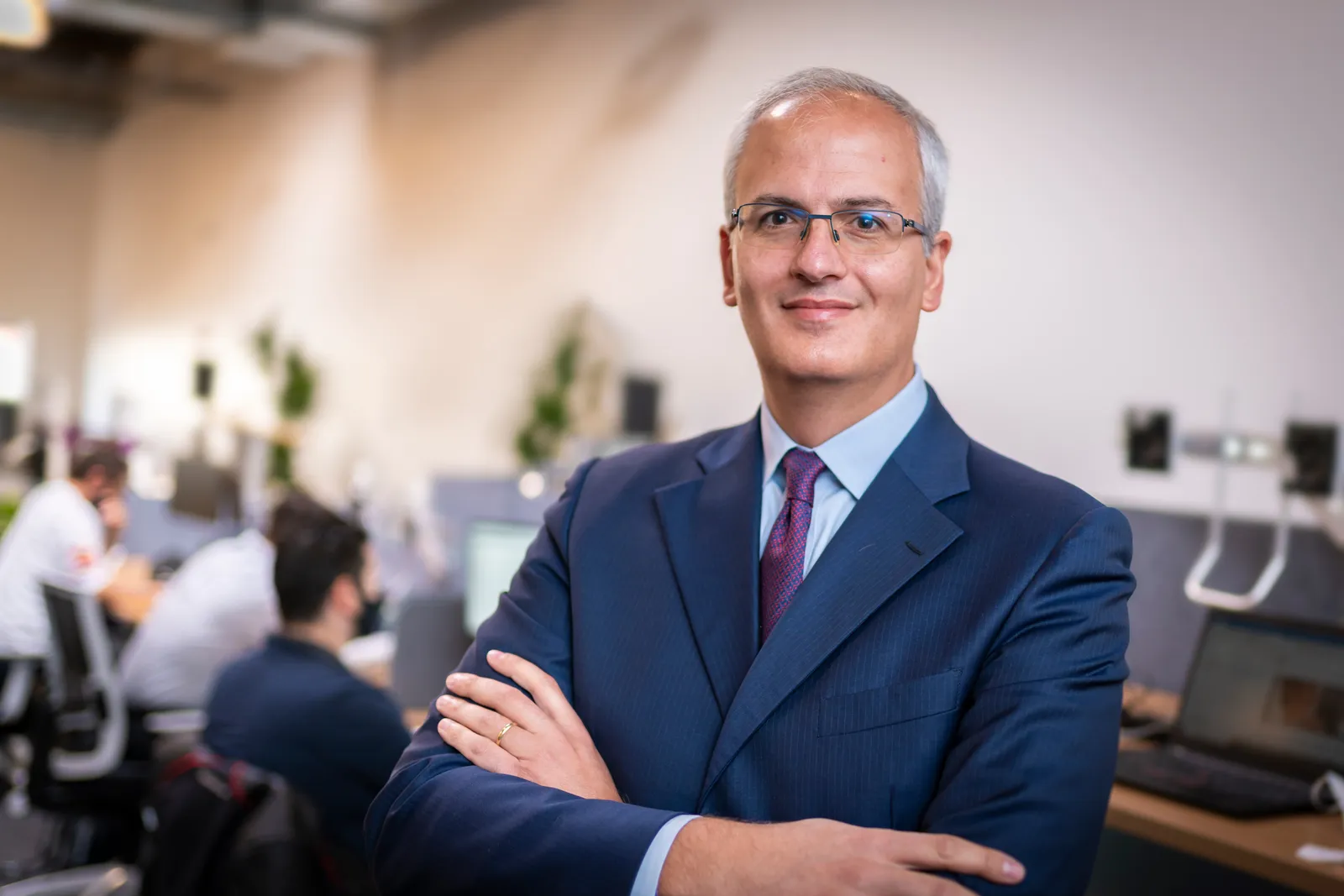
What are some other factors that are going into that decision process of choosing a site?
The main driver is the speed at which we will be able to deliver on the project. There is a huge demand for solar panels and the supply chain is facing disruptions for a number of reasons. But the incentives that have been put in place by the Inflation Reduction Act are going to increase demand and are going to help supply, so we see here an important window of opportunity and we want to be able to capture that as soon as possible.
For [the sites] that we're looking at, how fast can we get permits? Is this an easy site to develop or [does it have] additional complexities? How fast can we get the power upgrades to get the necessary power supply that we will need? Is there enough water and is it easily accessible? And then of course we look at is this site big enough, do we have access to a labor force?
What was the catalyst to launch this site at this time in the US? Was it the Inflation Reduction Act?
The [Inflation Reduction Act] is definitely contributing and is making us push on the accelerator as hard as we can. We started our analysis of the U.S. market to invest in the U.S. when the IRA was just more on the wish list. We have been developing and manufacturing solar panels for a decade now. Over the last few years, we have transitioned to the current technology that we are going to bring to market. Basically over the last couple of years we reached a maturity that we said, 'Okay, we are ready to go big with our technology with the level of proficiency and maturity that we have.'
So first we started because we saw that in Europe there was a real need for local manufacturing. I mean things like recent wars, disruption of the supply chain under COVID, political instability, political risks, especially in the supply chain of PV, which is highly dependent on a single geography globally.
And earlier this year we decided to expand our factory in Italy and increase it in size 15-fold. Once we had the blueprint in our hands, this is something that we can export and replicate elsewhere.
The U.S. was the first market we thought of. We are one of the largest renewable developers here, we know the market very well and the United States is one of the largest markets for PV. Earlier this year, we started our scouting for how we could bring our competencies here. Then the IRA arrived in August and immediately this became a very strong and appealing opportunity. Because the IRA incentives both on the demand side and for the very first time there were incentives on the manufacturing side that made the investment proposition much more effective and told us that we really need to be as fast as possible in the market.
Are you also building out the corresponding supply chain that is going to be needed to actually get these [products] to their endpoints?
Supply chain is critical, this business revolves around our ability to get what we need for our manufacturing. We start with silicon wafers. We're not getting farther down the supply chain because we don't have those competencies. We are working with a number of partners who have those capabilities and are willing to invest to create a new capacity for the manufacturing of silicon wafers. And we are in conversations with a few parties to secure the critical supply of wafers that we need, ensuring that the entire supply chain is fully traced, that we know exactly where every component is coming from.
And we are pushing to have, as much as possible, a local supply chain both in Europe and the United States. We are trying to get together with partners and suppliers to develop as much as possible a local supply chain for the physical components.
We've seen what kinds of headaches complex supply chains can give you in moments of disruptions, so we'd like to have everything as close as possible.